8 Fascinating Things I Learned From An F1 Factory Tour
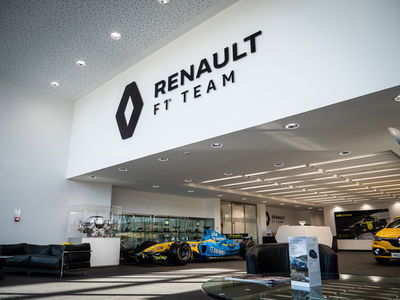
The F1 world is on pause right now. Covid-19 has caused the cancellation or postponement of multiple races, and the teams have all been shutting down their facilities to limit the spread of the disease amongst employees.
It’s a tough time for the sport, but rather than focusing on the tribulations of working against a global pandemic, we thought we’d provide a look at how an F1 team’s headquarters operates in happier circumstances.
Around this time last year to coincide with the UK launch of the Megane RS Trophy, Renault F1 gave us a tour of its Enstone facility. We were lead by Head of Technological Partnerships Luca Mazzocco, who’s been with the outfit over 23 years.
Here are some of the fascinating things we discovered:
Less wind tunnel use means more CFD
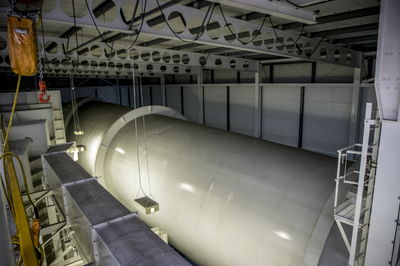
The air initially generated by Renault’s huge wind tunnel is too turbulent to be of any use, so it’s directed into a settling chamber. In here, turbine blades smooth it out into fast-moving laminar airflow which can be directed at a 60 per cent scale model. This air shoots out at 50 metres a second, which as Mazzocco gleefully points out, would probably kill you if you stood in front of it.
As you’d expect, it’s not the cheapest piece of equipment to run. So in the interests of cutting costs, the FIA currently limits how often and how long it can be turned on for. In response, the teams merely put more effort into Computational Fluid Dynamics, with Renault’s CFD efforts generating 60 terabytes of data every week.
“There are people [within the FIA] with good intentions, and they come up with a rule to try and limit costs, but they fight against some of the most competitive and clever engineers in the world,” Mazzocco said, adding, “The combined brainpower of all the teams together is a lot stronger than the FIA! It’s inevitable that people will find ways around it”. That’s a theme that seems to run through the whole factory tour.
Billions of race strategy simulations happen every year
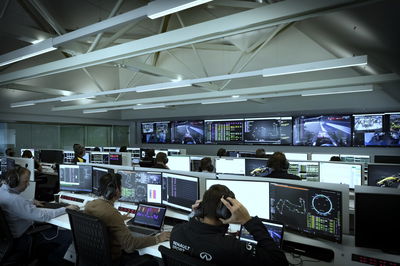
Another way the FIA has sought to limit costs is by restricting the number of personnel that each team can bring to a race weekend. And guess what? The teams found a way around that, too. The vast, screen-heavy Race Control Ops room can be filled with all the bodies Renault would ideally like to fly to the races, with myriad video feeds making it just as though they actually have.
“A guy in the gearbox can send an optical probe inside and send the images here on a screen - it’s better than being there because you haven’t travelled - you’re a lot less tired, you’re in an air-conditioned room,” Mazzocco explained. The room is at its busiest on Friday, being the ‘big engineering day’ of the F1 weekend.
To supply comprehensive data to both the Race Control Ops centre and those in the pits at the track, each F1 car is littered with 200 sensors. There are even sensors in the drivers’ gloves, to ensure medical staff on the ground know how serious things are if there’s been an incident.
The most fascinating fact of all we’re given in Ops relates to race strategy. There are 40 billion race strategy simulations every season, with 40,000 race outcome possibilities crunched by Renault F1’s computers every single lap of the Grand Prix.
3D printing is used for the car, the wind tunnel and more
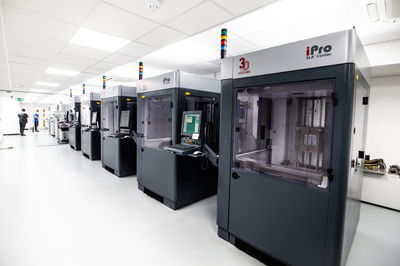
3D printing is becoming increasingly important for Renault and the F1 world as a whole. Along with components for the car itself, additive manufacturing is now a vital tool for making prototype parts. Mazzocco uses the example of a part which could take 20 hours of CNC milling over several weeks to complete - if the end result is no good, all of that time has gone to waste. Instead, a replica could be 3D printed in just a few hours, and all being well, validated ahead of the real deal being produced.
It’s even better for making parts for wind-tunnel testing. Previously, parts made from carbon fibre and aluminium where used, presenting a number of problems. Firstly, that’s a resource-heavy way of doing things, limiting the amount of parts that can be tested. Secondly, with metal and carbon parts, it’s difficult to embed sensors - a lot of messy and time-consuming drilling can be involved.
With 3D printing allowing for channels for sensor equipment to be woven through the prototype parts as they’re made, it gets a whole lot easier. Mazzocco showed us a radiator for the wind tunnel model, complete with 32 built-in measuring points, out of a total of 350 over the whole replica car.
On our TV screens, F1 cars appear to move around with an almost graceful smoothness. What’s going on inside the car, however, tells a different, more violent story. Suspension components need to be testing to withstand the extreme forces an F1 car is put under, something the seven-post rig is used for.
So-called because of the seven points of the machine that are attached to the car, it replicates the pitch, yaw and even the downforce that’ll be experienced IRL. It’s not random, either - the system can replicate different circuits, and even different driving styles.
Fernando Alonso is said to have visited the facility during his time at Renault F1, and after observing the machine at work, noted, “That’s Spa and it’s me driving”. And yes, he was spot on.
F1 car ballast is as dense as uranium
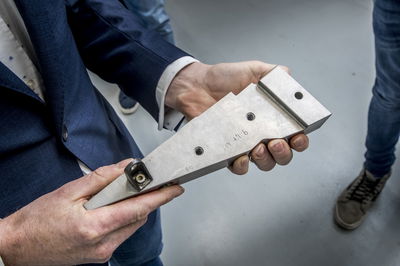
F1 teams commit vast resources to make their cars as light as possible - preferably under the minimum weight mandated by the FIA. Renault’s machine shop gives a few examples of how this is done, including the exhaust systems (hand made, as is everything in this part of the factory), crafted using Inconel with a thickness of 1.1mm. Before the turbocharged, hybrid era, this was down to just 0.5mm.
Being under the weight limit, of course, means you then need to… add it back on again. “It sounds stupid - why do you waste a lot of money, and then you add weight? But this way you put it where you want,” Mazzocco explains. The ballast is made of a tungsten alloy that’s as dense as uranium, so as well as aiding weight distribution, the strategic placement of it can reduce the centre of gravity.
It has several pharmaceutical standard cleanrooms
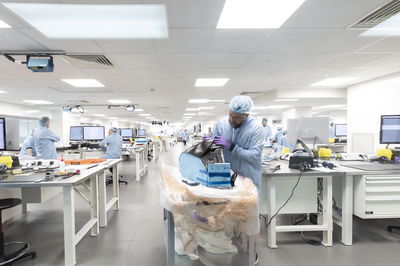
Enstone has several cleanrooms that are classified as ISO 7, which is typical of what you’d find in the pharmaceutical industry. HEPA filters drastically reduce the amount of particulate matter that goes into the facilities, and the air is replenished an average of 30-60 times an hour, compared to just 2-4 times in a conventional room.
One of the cleanrooms is used to laminate carbon fibre ply using a laser-guided machine before the chunks of CF are sent to the ‘autoclave’ for cooking. Nearby, you’ll also find a CT scan machine and an X-ray used to inspect parts for defects, mirroring similar processes used by the aerospace industry.
Simulators are key in part development
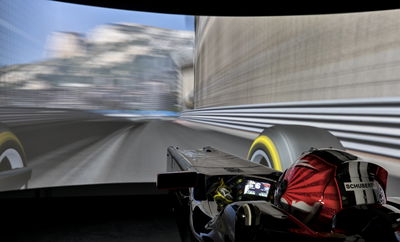
Wind tunnel testing and CFD can only tell you so much about the aero on the car. In an ideal world, you’d get new parts on the vehicle ASAP and test it IRL, but that’s not so easy given the testing restrictions imposed by the FIA. “Before we had double [the] trucks, double [the] mechanics, double [the] engineers, so the driver could fly straight from a race to a test on the other side of the world,” Mazzocco recalls.
This is another one of those cat and mouse situations between the sport’s governing body and the teams. As soon as the FIA stopped them spending so much money on real-world testing, a shed-load of cash was invested in simulation as a response.
Renault’s setup involves five projectors, a powerful motor to give force feedback to the steering wheel, and virtual tracks supplied by R Factor Pro. The system is sophisticated enough to simulate the effects of any new parts the team might be working on, allowing drivers to give something close to real-world feedback.
Parts are signed off at the very last minute
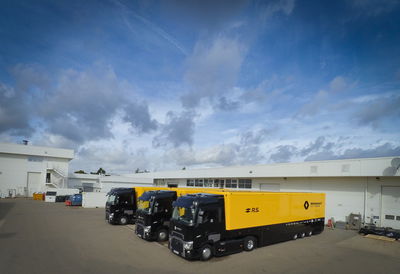
After a final inspection process, parts are signed off and ready to go in the car. But just because the containers (for flyaway rounds) or trucks (for European events) have left Enstone, that doesn’t stop the supply of new bits.
Since he isn’t an engineer, Mazzocco arrives at the race locations later than many of his colleagues, making him the perfect ‘mule’ to cart over last-minute additions to the car. And there are a lot of them. “In Australia [2019] I arrived on Wednesday with 15 suitcases, and then on Thursday Friday and Saturday the same number of suitcases were arriving with other colleagues,” he recalled.
Mazzocco was held back as long as possible before departure, too. “My taxi was waiting but I couldn’t go just yet, because they were still printing the part numbers on some of the last components!”
Comments
Its amazing how much stuff they can do give them a problem and in less than a week they will solve it, Mercedes and the CPAP device for example, there are LOADS of brainy people inside an F1 team, its just amazing to see all of this talent there knowing they are fighting for tenths of a second its awesome
Just watching that seven-post rig video makes my back hurt.
i would recommend you to check https://expomovers.com/ which are the best moving company inside new york city. They have a lot of great cars to move your staff from one place to another.